Spring Break: How to avoid spring brake downtime in bulk hauling applications
There’s not really a “typical” bulk trailer hauling job, is there? From the trailer type to the job site surroundings to the cargo on board, no two situations are ever quite the same.
But in every case, there’s a common factor that’s probably being overlooked when it comes to improving safety and uptime. When was the last time you thought about spring brakes? Unless they required replacement, it’s probably been a while. That makes now as good as any time to remember what’s at stake when it comes to extending spring brakes’ lifecycle, protecting their performance, and selecting the right type for an operation’s trailers.
Key components in safety
We’ll level-set with a quick look at what’s inside a spring brake and how it works. Responsible for both service and parking brake applications, a spring brake comprises two sides: the service chamber side, which is used to slow or stop a vehicle; and the parking side, which holds the vehicle in place when it’s parked. The parking side also works as a fail-safe if the air brake system loses pressure, and within it is a large power spring.
This spring is compressed under normal operating conditions while the vehicle is in motion, but once it’s parked, the spring is released, delivering the braking force to hold the vehicle in place. Engineering this spring for maximum durability is crucial since the longevity and operability of the brake rests on its ability to maintain this force over time. The leading cause of spring brake malfunction is a broken power spring—and if it fails, downtime is in the vehicle’s future.
So, what keeps a spring brake from reaching its expected product life, saddling fleets with unplanned garage time and maintenance costs?
What makes a brake break?
The most common causes of broken power springs are moisture and contaminants getting into the brake chamber and causing corrosion that weakens the spring. Most North American trailers encounter these in the form of road salts, but bulk trailers can face a much wider range of hazards in the normal course of operation, such as going off-road onto construction sites or gravel pits. Different trailer designs can put the chambers in closer contact with corrosive materials, as can jobs that require repeatedly backing up or driving over these materials.
This exposure often occurs due to the design of a vented spring brake, which includes drain holes that permit air to escape when the parking brake is released. The danger is that they also make it possible for contaminants to get in. Once inside, contaminants will begin abrading the coating, leading to corrosion of the power spring. Additionally, some materials—limestone, for example—can get wet and then harden in or on the spring brake while drying, becoming exceedingly difficult to remove. Always be cautious about introducing pressure washing to remove these materials, as this action can introduce caustic detergents to the mix through the drain holes.
Locking out contaminants
Sealed spring brakes are engineered to help prevent contamination from happening. Bendix’s design—the EnduraSure Pro—uses a one-way check valve integrated into the dust plug and eliminates the drain holes. This way, the brake can keep contaminants out while still “breathing.” And since they protect the power spring, sealed spring brakes are a great choice for all applications, especially those in severe service and bulk applications in which trailers are exposed to high levels of dust, aggregates, or other potential contaminants. Equipping long-lived trailers and tankers with sealed chambers can deliver the dual benefits of longer service intervals and extra protection for trailers that are parked for extended periods, since those wheel-ends can be more susceptible to collecting moisture when standard spring brakes are used.
When selecting spring brakes for the fleet, remain vigilant. Many marketers will describe spring brakes as “premium” even if they’re not sealed. And while almost all manufacturers will detail the protective coatings on their power springs, preventing a corrosive environment within the chamber in the first place is an even stronger deterrent.
Dig into the details
It’s important to consider other factors about the spring brake as well. For example, coil clash occurs when a power spring’s coils come into contact with each other and gradually wear away their protective coating, so be sure to ask whether the design prevents that. Also, look into the power spring’s shut height, a measure of how much the spring is compressed. A greater shut height means less stress on the spring, and over-compression can cause a decrease in the force output, reducing the safety margin when parking.
Bulk hauling applications can put a lot of stress on spring brakes, and sooner or later, they’ll all need replacing. When that time comes, the work put into making the right choice will pay off—in the form of improved service life, lower total cost of ownership, and safe, dependable performance.
Mark Holley is the director of marketing and customer solutions for wheel-ends at Bendix Commercial Vehicle Systems.
About the Author
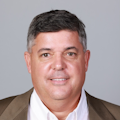
Mark Holley
Mark Holley is the director of marketing and customer solutions for wheel-ends at Bendix Commercial Vehicle Systems. Holley’s career as an accomplished professional with a broad range of practical business experience spans over 25 years in the commercial vehicle industry. He has held numerous key roles in operations, product marketing, and product management in the OEM and aftermarket segments.